Productivity Expert
SYNCHRONIZE your continuous improvement activities of your MANUFACTURING PLANTS
Fast return with LEAN approch
With 28 years of experience in the manufacturing industry, I gained a deep understanding of modern plant operations and financial management. Combined with the multitude of continuous improvement interventions carried out, this allows me to quickly target the actions to be taken in order to obtain the desired gains.
I will quickly accompany you towards increased productivity.
My track record demonstrates it, I transfer knowledge to your team, in order to create a sustainable methodology and culture for your company. The gains made will become the basis for the future.
Try it out.
Try it out.

To reach your goal quickly, measurement tools are essential.
Are you using the right ones?Call us. We know how to get you there
My expertise
The transfer of knowledge provides undeniable gains.
My deep experiences and my passion for the manufacturing industry, supported by my technical skills in plants like assembly, manufacturing, slaughterhouse, meat plant, food processing, packaging, paper converting, pulp and paper, printing, plastic molding and medical components fabrication will bring you the desired gains.
I guide you in improving your overall performance. These changes are customized for your business to increase your bottom line without capital injection.
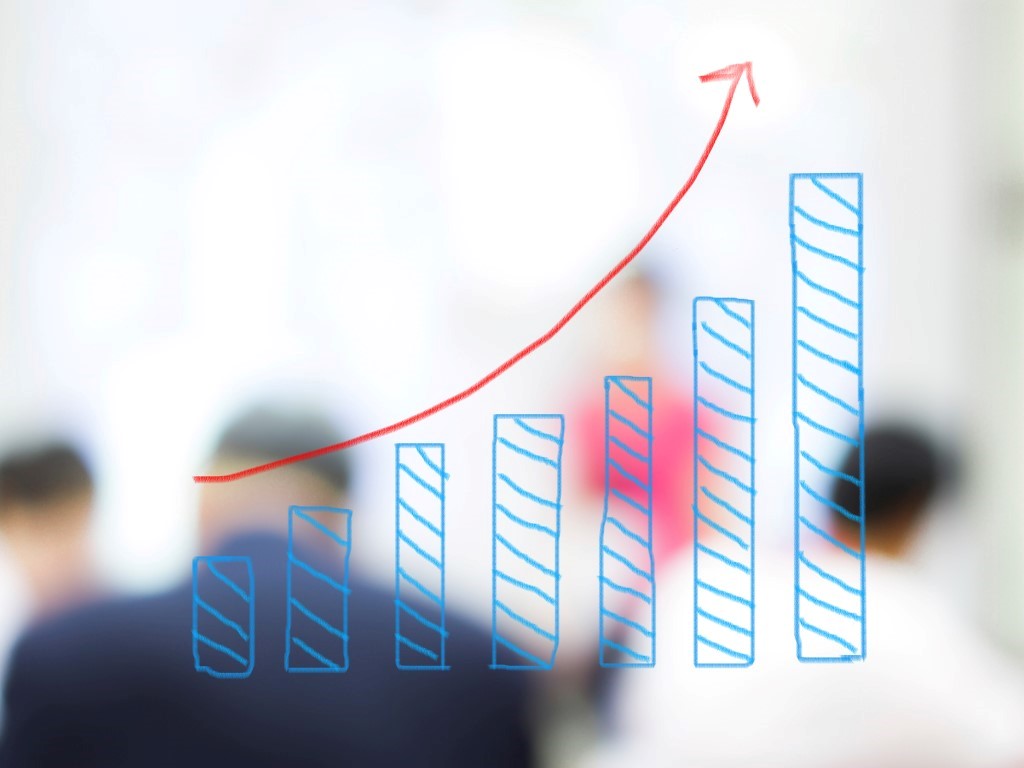
- Assessment of height types of waste and improvement
- Improved productivity
- Performance analysis (KPI)
- Improved manufacturing delays
- Temporary replacement of resources
- Temporary management and supervision
- Evaluation of operational performance
- Implementation of new business processes
- Working together with suppliers to improve performance (quality, time, cost)
- Stock level evaluation and reduction
- Shortage management
- Cycle counts implementation
- Temporary replacement of resources
- Standardized production methods to guarantee quality the first time
- Standard documents and training support tools (assembly lines, manual operation, training videos, etc.)
- Implementation and training of work teams
- Optimization of flow and plan layout
- Tooling design (poka-yoke)
- Time management (timing)
- Optimal workflow (sequence of work)
- Levelling the work load
- Performance analysis (KPI)
- Improvement / implementation of business processes
- Use of lean tools (5S, SMED, etc.)
- Temporary replacement of resources
- Purchase and installation of new equipment
- Plant layout
- Plant capacity (evaluation and management)
- Temporary replacement of resources
- Temporary management and supervision
- Analysis of causes of downtime
- Increased availability of equipment (Preventive Maintenance)
- System implementation (CMMS)
- Key Performance Indicators (KPI)
- Key Performance Indicators (KPI)
- Mobilization and hands-on training
- Root cause analysis to reduce incidents and accidents
- Culture health and safety
- Assessing risk and deploy action plan
- Lock out and tags out procedures
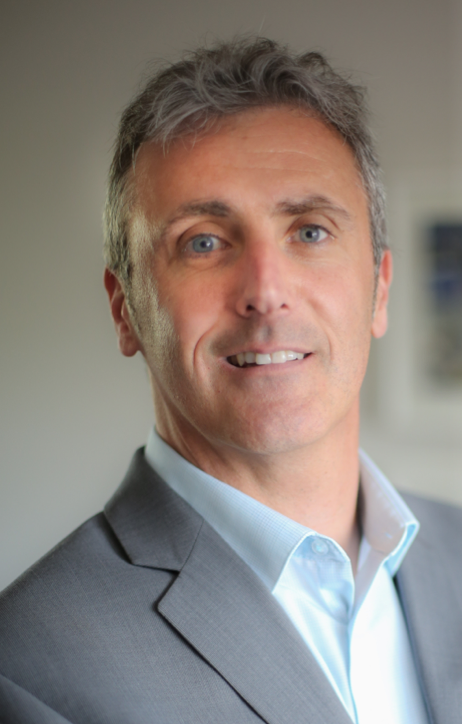
Luc Chouinard, P. Eng.
Productivity Expert
Consulting services for Manufacturing Industries
514 402-9335